Productivity Through Innovation: Giltbrook Dyers and Cleaners Ltd
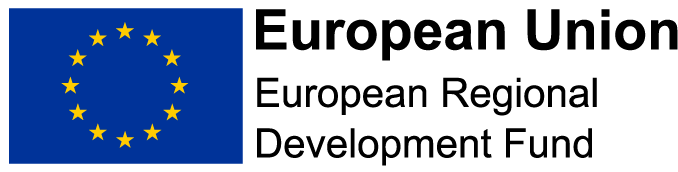
Giltbrook Dyers & Cleaners Ltd (T/A Giltbrook Workwear) has been providing sustainable workwear solutions to businesses across a range of sectors for over 75 years, from healthcare, construction and food manufacturing, to transport and universities including NTU.
The East Midlands based, family run SME is one of the leading workwear rental specialists in the country, with an in-depth knowledge of industry regulations, fabric durability and wearer comfort.
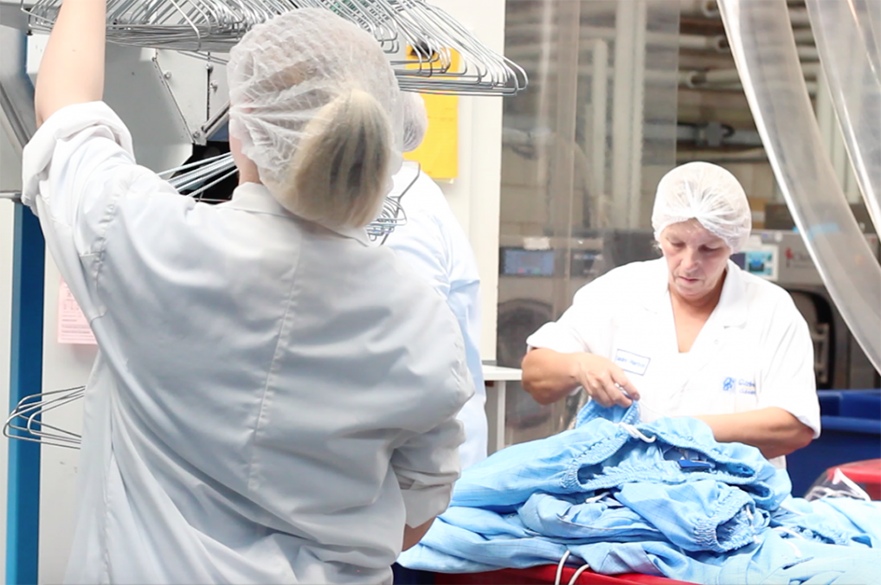
Bringing data to life for a pioneer of sustainable workwear
Giltbrook’s environmentally friendly commercial laundry facility accredited to ISO 14001 and ISO 9001 is among the most advanced in Europe. As well as providing workwear, the company collects, cleans, and returns thousands of items direct to individual staff lockers – maximising the lifetime of every garment through a sustainable, circular process.
Items are tracked as they go through the laundry, using radio frequency identification transponders and barcode technology, to make sure they’re cared for to the highest standard in line with each customer’s specific needs. The facility also uses sustainable techniques such as their Solar generation system, rainwater harvesting and rinse water recycling.
Data-driven productivity
Via NTU’s Productivity through Innovation project, CEO Chris Jackson has been working with software development specialists from NTU, Nigel King and Alaa Bafail, to develop a software development strategy focused on making efficiencies and improving productivity.
As part of the project, the firm has been supported to research tech stack options for a database dashboard that will reduce the need for manual inputting of data, improve data accuracy, and visualise KPIs such as carbon reduction targets to share with the wider business. The support included recommended approaches and help with the scoping, specification and tendering process.
We spoke to Chris in March 2022 to find out how his business has benefited from the support on offer.
"As a business, we’re good at collecting data. We’ve been doing it on a weekly basis since 2007, to give us a weekly snapshot of how we’re performing against our KPIs, based on information gathered from across the company. We monitor everything from laundry water use and effluence, to onsite generation from our 50kWh solar panel system, to productivity and financial data. 40% of our electricity is generated onsite, which is a big help in terms of rising energy bills.
"Historically, we’ve used Excel to enter these different inputs but it’s an ongoing challenge to make sense of the sheer amount of information we’re collecting. We’ve been looking at ways to streamline the process and make it easier to enter, analyse and visualise our cauldron of data – so we can act on it quickly.
"We need to move from Excel to a database dashboard system, to bring our data to life and gather information from a range of interconnected, networked sources – the Internet of Industrial Things (IIoT). For example, the sensors we use in our laundry to monitor outputs such as energy, water and effluent.
"Monitoring that data via a dashboard will help us develop and continually improve our processes and measure the impact of incremental changes. If we change the temperature on our laundry boilers, how will that impact wash quality? Or, if we change the washing process, how will that effect our gas , water & electricity consumption? We need accurate data to make the right decisions.
"Nigel and Alaa have supported us to find the right database dashboard system. They started by looking at what we’ve already got, and what we value as a business, and then ranked the different technologies available, based on a framework criteria we developed together.
"Working with Nigel and Alaa has given us the ability to really step back and take the time to assess the benefits of each approach, against key factors like the cost, time and resources involved.
"They have been a great ‘critical friend’ and have supported our conversations with private sector software providers. It’s good to have an independent view and be able to learn from Nigel and Alaa’s experience in other sectors. It’s brought ideas to the table that we wouldn’t have thought of and helped to challenge our thinking, preventing us from falling into the trap of going down a path which isn’t right for the business."

The impact
"With NTU’s support, we’ve achieved our goal of thoroughly assessing what’s out there in the market, and have a more realistic expectation of the cost, time and technical challenges involved. The technology we use to digitise our processes means there are lots of different variables to consider.
"As an SME, we have limited resources and don’t have the financial ability to recruit a technical director or hire consultants, so working with NTU has given us an invaluable extra resource. We’re now looking at the next stage of scoping the project ready for tendering, building on the work we’ve done with Nigel and Alaa.
"The framework criteria and rationale we developed together will underpin and reinforce our decision-making process as we move towards scoping and tendering.
"Nigel and Alaa have helped us look at each stage of the process, including cleansing our data, rethinking how it’s organised, and designing the outputs we need, which will save us cost and time further down the line. Now, when we put out a tender, we will be confident it’s well thought out and right first time. Any business is only as good as its suppliers, which is why taking a strategic approach to assess our options has been so important.
"The system we want would cost tens of thousands of pounds, which as a SME would usually be beyond our capability. Crucially, with Nigel and Alaa’s help, we’ve developed a clear business case for the project, which means we can apply for government funding for green and digital manufacturing. The right database dashboard system will help us improve our business processes, increase productivity, visualise our carbon impact, and report on our KPIs to our board, staff and customers.
"As a member of the Textile Services Association’s (TSA) PPE forum, I’m really interested in how our sector can use data to improve transparency and show customers how we’re moving towards net zero. Our software development strategy isn’t just about choosing the right system. It will enable us to grow and thrive in a new era of sustainable, digital manufacturing."
Get in touch
Giltbrook Dyers and Cleaners Ltd has benefited from support through the Productivity through Innovation project, which is part-funded by the European Regional Development Fund (ERDF).
If you have a ‘productivity’ challenge and would like support, email the PTI Team PTIAdmin@ntu.ac.uk